Fig. 5.1
The major 3D printing technologies reviewed in this chapter, organized hierarchically by enabling technology, delivery system and available materials for each system
Fused Deposition Modeling (FDM)
Fused deposition modeling—also known as fused filament fabrication (FFF) and plastic jet printing (PJP)—was first developed in the early 1990s by Crump [6], who went on to found the 3D printing company Stratasys. While Stratasys still technically trademarks the abbreviation for fused deposition modeling (FDM) over the past decade, it has come to be ubiquitously associated with a class of 3D printers that produce objects through the successive layering of a thermoplastic, and we will use that abbreviation for this chapter.
Thermoplastics—Enabling Technology of FDM
Thermoplastic materials are at the heart of FDM technology. These materials are capable of being repeatedly melted and re-solidified by the exposure and removal of heat [7]. FDM takes advantage of this property by feeding a thin (typically 1.5–3 mm in diameter) filament of thermoplastic into a heated nozzle (or printer head) from which the melted plastic is then extruded through an opening a few hundred microns in diameter (most are 100–500 microns) (Fig. 5.2a). Upon extrusion, the thermoplastic material quickly returns to a solid state, which allows FDM printers to achieve layer-resolutions (layer heights) on the order of tens of microns. Such a rapid transition from solid to liquid (or semisolid) and back to solid is enabled by keeping the temperature of the nozzle at or close to the glass transition temperature of the material being extruded. At this temperature, the thermoplastic is heated enough to flow through the printer head of an FDM printer in a semi-liquid manner, but also cool enough to rapidly return to solid state temperatures once it is no longer in direct contact with the heated extrusion assembly.


Fig. 5.2
a A diagrammatic representation of the FDM printing process, showing the extruder, print head and print head motion, as well as the layering method used by FMD and a schematic representation of a part that includes overhang and supports. b, c Two examples of the trabecular-structured infill used by FDM 3D printers. b shows a dense, rectilinear infill pattern while c shows a sparser, hexagonal infill pattern
In order to actually print with this method, the printer head is attached to a mechanical chassis comprised of motors that use belt and/or lead screw systems to move the extrusion assembly in a 3-dimensional, Cartesian system (i.e. X-, Y-, and Z-axes). In addition to the three Cartesian motors, a fourth motor is used to advance thermoplastic filament into the printer’s heated nozzle. Coordinated control of these four motors (typically abbreviated as X, Y, Z, and E) by a computer allows the printer head to rapidly move through 3D space while continuously extruding melted filament (Fig. 5.2a).
FDM Method of Printing and Design/Manufacturing Considerations
While an FDM printer head is capable of simultaneously moving in X, Y, and Z, these printers only print in two-dimensional layers at a time. To produce a three-dimensional model, FDM printers print successive layers of thermoplastic that can be thought of as two-dimensional cross-sections of the whole three-dimensional model. The first layer of an FDM print is deposited onto the bed of the 3D printer—which is typically made of metal, ceramic, or hard plastic—and each successive layer is deposited on top of the printed layer beneath it. Thus, at any given time, an FDM 3D printer is usually printing only a 2D layer on the X/Y plane for some Z height, only briefly pausing extrusion to advance one-step up to the next Z height to print that layer’s 2D cross-section.
An important manufacturing contingency for this method of successive layering requires that the material deposited on each layer has something to rest upon beneath it, be that the printer bed or a previous layer of material. If a significant portion of a subsequent layer has no material to rest upon from the previous layer, typically referred to as “overhang,” that portion of extruded thermoplastic will be unable to maintain its intended structure and instead “droop” downwards. Since, by design, some 3D models must include overhanging structural features, FDM printers are capable of additionally printing struts of material beneath these features for support, as depicted by the lighter colored, vertical bars in Fig. 5.2a. These struts, known as “supports,” can be printed from the same material as the model and then removed after printing using cutting tools and brute force. They can also be printed from a soluble thermoplastic that is deposited by a second extruder during the print, if present, allowing the supports to be dissolved in a particular solvent while leaving the model intact.
FDM Output Considerations—Layers and Infill
Overhang and supports are two of several manufacturing considerations that are involved in the determination of how to print a 3D model using FDM (and other types of 3D printers as well). Two other important output parameters include the height of each layer and the amount of infill material printed on each layer.
Layer height directly translates to the amount of distance the Z-axis motor will move the head upwards per cross-sectional layer of the model. For example, a layer height of 0.2 mm means that after printing each 2D section, the printer head will move up 0.2 mm and then begin printing the next layer of the model. Layer height can also be thought of—and is often easier to translate back to a 3D model—as the spacing between the planes that will slice the 3D model into its respective 2D cross-sections. As one might expect, the larger the layer height, the lesser the printed model can capture small changes in the profile of a model. A 3D model with a sinusoidal profile will be smoother when printed with a layer height of 0.1 mm versus that same model when printed with a layer height of 0.3 mm, since more points along the sinusoid can be captured if the model is printed in increasing increments of 0.1 mm versus increasing increments of 0.3 mm. In exchange for a loss of resolution, however, a model will take less time to print using a larger layer height compared to that same model on a smaller layer height, since the printer head will have to make fewer passes in order to complete the total height of the model. In several other forms of 3D printing discussed later on in this chapter, layer height is also a printing parameter than can be adjusted for each printing job. As is the case with FDM, there is a degree of tradeoff between time and model accuracy that accompanies a given layer height.
FDM printing also provides users with the capability to adjust how a printer will pattern each layer of a model. Since the material from which the model is constructed is only deposited from the printer head, a 3D model does not need to be made out of solid thermoplastic. Rather, a semi-hollow, trabecular structure (Fig. 5.2b, c) is often used in FDM in order to reduce the weight of the part and the amount of material needed to produce it while also maintaining strength and form. The density of that trabecular thermoplastic structure (infill) can be adjusted by the user depending on the function and performance of the printed model. With the exception of the first few and last few layers, which are printed as solid thermoplastic, all other layers of an FDM printed model are produced by first tracing out the perimeter of that layer and then filling in the space enclosed by that perimeter with an alternating pattern of material and space. The most common patterns used by FDM printers are hexagons (Fig. 5.2c), rectangles, and parallel lines (Fig. 5.2b), but more playful internal patterns, such as cat outlines [8], can also be produced (if desired). As layer height corresponds to model resolution, infill density corresponds, generally, to model strength—a model printed with an infill density of 100% (effectively solid) will be able to withstand more mechanical stress than that same model printed with an infill density of only 10% (90% of the internal space of the model is empty).
FDM Materials
FDM is one of the most versatile forms of 3D printing, with respect to materials selection. Unlike other forms of 3D printing, which are limited to a single class of polymeric compound, the exclusively physical phase changes associated with FDM materials allow the technology to make use of a wide array of materials with vastly different properties with minimal adjustment to the 3D printer. Fundamentally, any thermoplastic is a candidate material for FDM (of which there are about a dozen available) including poly-lactic acid (PLA), acrylonitrile butadiene styrene (ABS), polycarbonate (PC), thermoplastic urethane (TPU), and polystyrene. For the purposes of descriptive modeling where material properties are less important than model geometry, the most common materials such as ABS and PLA will usually be sufficient.1
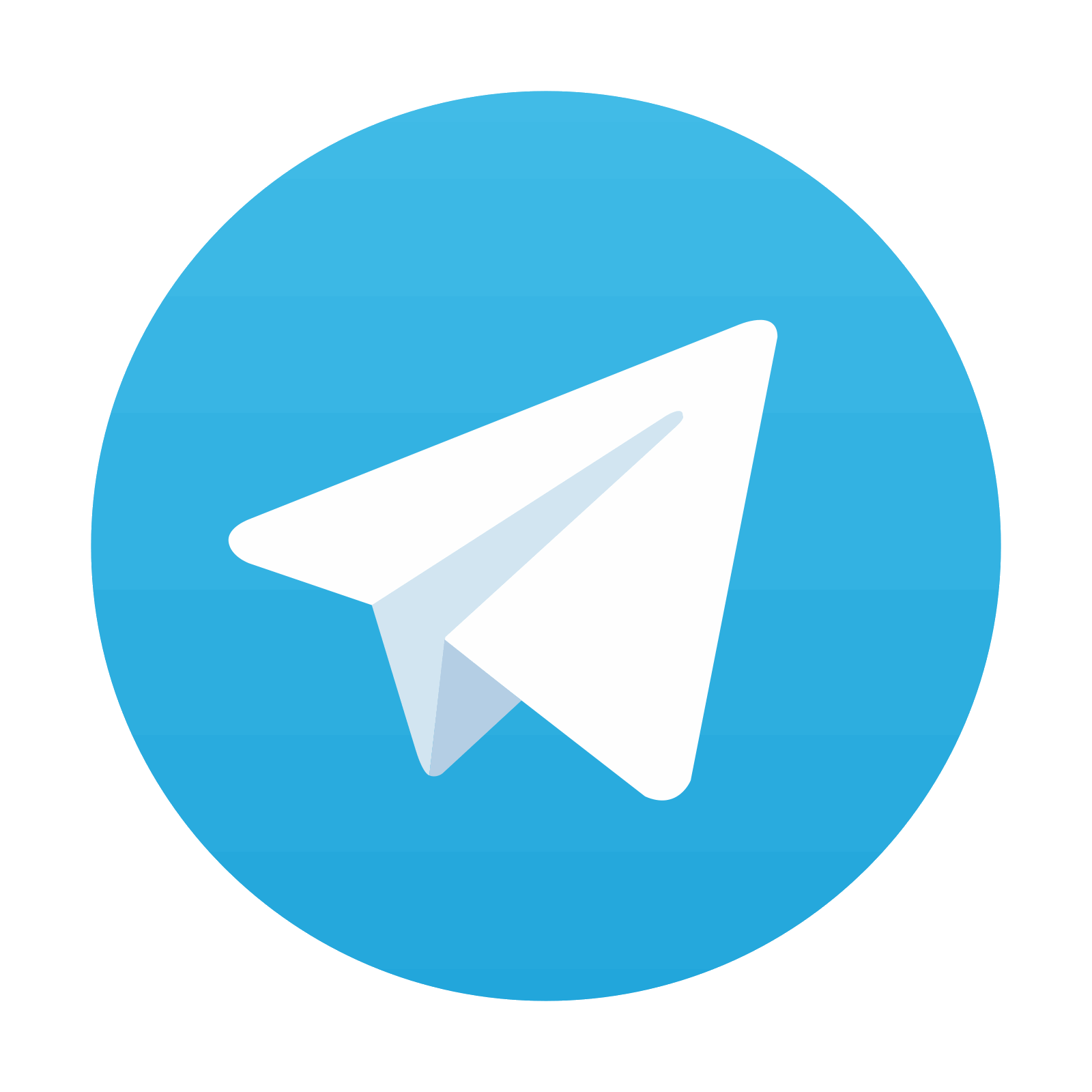
Stay updated, free articles. Join our Telegram channel
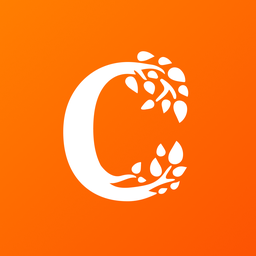
Full access? Get Clinical Tree
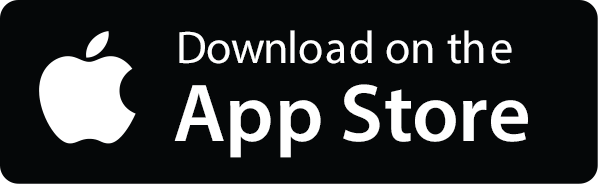
