19
Work with electronics
The most common respiratory problems in the electronics industry are caused by inhaling fluxes used for soldering.
Soldering has taken place since ancient times. The first written account is in 77AD in Pliny’s Naturalis Historica. He describes the soldering of copper with cadmea (zinc oxide) with lead resin (probably colophonian) or white lead (tin). At that time, the resin was produced from a number of different species of pine and birch, one of which was the colophon pine. Between 800 and 1100 AD the Mappae Clavicula, a written set of workshop instructions, included one form of solder cream whose recipe translates ‘take two parts of axle grease and a third of resin, mix with an equal quantity of tin filings, heat as you know how and a joint will be made’. In about 1125 a monk known asTheophiluswrote afirst-hand account of solderingin thejointingoftinwhich,after heating the tin, involved smearing it round with the resin of a fir tree. In 1360 Bartholomew Granville wrote an encyclopaedic book called De Proprietatibus Rerum, which states that the jointing of metals ‘may not be foundered without tallow and rosen’.
Soft soldering is therefore very ancient. Colophony has been recommended as a flux at least since 1150 and has been the standard flux for the electronics industry since the 1930s. Activators are now added routinely to the colophony to hasten its action. Since about 1980 there have been attempts to replace the colophony in soldering fluxes with a number of other materials, many of which are less easy to use.
19.3 Diseases in those exposed to soft soldering flux fumes
Pliny notes that colophony is yellower than ‘the rest but if ground up turns white; it has a rather oppressive scent and consequently the perfumers do not make use of it’. There is then no mention of health hazards until, in 1967, an outbreak of respiratory disease amongst coil winders and tinners in an electronics factory in Monkstown, Northern Ireland. Thirty-nine women and one man in a factory employing 700 were affected with breathlessness and cough. The attacks occurred at work and at night in bed, and were associated with fever and sweating. Polyurethane-coated wire had recently been introduced for coil winding and isocyanates were detected in the fume. The outbreak was attributed to isocyanate sensitization without further investigation; the workers were also exposed to colophony fumes. The first bronchial provocation testing for isocyanates in electronics workers was in 1972, when isocyanates were shown to be the cause in a solderer and wirer and a supervisor working in an electronics factory.
The occupational exposure standard for colophony exposure was based on a study by Christy in 1973 following respiratory problems in an American telephone factory where 25 people were restricted from working in the soldering area because of upper respiratory irritation. The exposure standard first proposed 5 years earlier was developed following the exposure of 18 asymptomatic volunteers to heated colophony fumes for periods of 15 minutes and was based on the level required for irritation to the eyes, nose and throat. As an assay on resin acids was not available, the aldehyde content of the fume, expressed as formaldehyde, was initially set as the item to be measured (to make the measurement in mg/m3 a molecular weight of the aldehyde needed to be used; formaldehyde is the lowest molecular weight aldehyde and was used for convenience). This caused great confusion, leading to the belief that formaldehyde was the agent responsible for the adverse reactions to colophony, rather than the resin acid content of the fume, as subsequently demonstrated.
Occupational asthma due to colophony fumes was first reported in 1976 from Moscow and London, both with positive bronchial provocation tests to the colophony based fluxes. All patients were wirers and solderers in different factories.
There are a number of other soldering fluxes that have (rarely) caused occupational asthma. They include dodecanediotic acid, polyether alcohol-polypropylene glycol and adipic acid. Corrosive fluxes containing zinc and ammonium chloride have caused asthma; however, these are usually used for plumbing rather than electronics as their residues are corrosive and need washing off after soldering.
There are many millions employed in the electronics industry worldwide. Basic manufacture involving large workforces, such as soldering operations, has moved from high-income countries to low-income countries. Most of the literature is from the former but it is likely that adverse health consequences are at least as frequent in lower-income countries.
19.5 Definition of scope (and limitations)
This chapter concentrates on occupational asthma. The main causes in the electronics industry are colophony and to a lesser extent isocyanates and acrylates, often used for encapsulation. Recent work on indium alveolitis is included; as far as is known, this is a rare disease and does not fit easily into the usual classification of interstitial lung diseases. There is little information on other respiratory hazards in the electronics industry.
19.6 Exposures and processes in the electronics industry
Printed circuit board manufacture includes resin bonding, impregnation, laminating, photomasking and etching, cutting and drilling, marking and testing. During preparation, boards may be cleaned with persulfate salts, recognized as potential respiratory sensitizing agents. Once prepared, the circuit boards are then assembled with components which need to be soldered into the printed circuits. This process may be enclosed in automatic flow solder machines, or may involve hand soldering, particularly when rectifying faulty connections. The solder flux fumes are the major hazard, but rectification may involve using a soldering iron to burn through a surface coating, which if encapsulated by polyurethanes may liberate isocyanates. The board is then ready for assembly into the final product.
Semiconductor wafer manufacture is where circuits are etched onto silicon wafers. Processes include crystal purification and growth, wafer preparation, epitaxy1 and oxidation, photolithography, doping and type conversion, metallization, interconnections and packaging. This is followed by the assembly of the semiconductors including die separation and bonding, wire bonding, encapsulation, marking and testing. The encapsulation process may involve isocyanates, acrylates or epoxy resins, possible causes of occupational asthma (Table 19.1).
19.7 Practical hints (and pitfalls) when taking a history from patient
- Colophony is often called rosin. It is the same material that stringed musical instrument players put on their bows to increase friction, and it used to be used in older adhesive dressings. Resin is a less specific term which includes colophony.
- Many workers exposed to solder flux fumes get their exposure as bystanders rather than by performing soldering themselves. Some surveys have found the prevalence of occupational asthma to be as high in bystanders as in those soldering.
- Hazard labels on solder are often concerned with its lead content. The usual electronic solder is a mixture of tin and lead, neither of which is volatile at soldering temperatures of 250-350 C; lead poisoning is not a problem in electronics workers. The volatile products come from the fluxes which are needed to exclude oxygen from the heated metals to be joined and to assist the flow of the solder.
- Not all electronic solders contain colophony, and not all colophony-free fluxes are completely free of colophony.
- Workers using colophony-free soldering fluxes may still be exposed to colophony when de-soldering equipment (during repairs) which was originally soldered with colophony fluxes.
- Exposure to isocyanates may occur when polyurethane coated wires are soldered, or soldering takes place through polyurethane encapsulation during repair work.
19.8 How to document exposure, including biomonitoring
Exposure to electronic soldering fluxes is usually fairly obvious, as a fume is required for successful soldering. Sometimes the soldering is automated and enclosed; exposure is then possible during breakdowns, or if extracted fume is recirculated into the work environment. Exposure standards are based on the total resin acid content of the fume, which requires gas chromatography and flame ionization detection. In the UK the workplace exposure limit is currently 0.05 mg/m3 and a 15 minute time-weighted average of 0.15 mg/m3 for short-term exposures. Biological monitoring is not in general use and is usually unnecessary, but it is possible in urine collected at the end of a shift. Analysis requires hydrolysing aliquots of urine at 90 C for 1 hour with concentrated hydrochloric acid, followed by extraction into diethyl ether and evaporated under nitrogen. The residue is then derived using methylformamide dimethylacetal and analysed by gas chromatography with mass spectrometric detection using positive electron impact ionization and selected ion monitoring. An 8 hour exposure at the workplace exposure limit of 0.05 mg/m3 equates to a post-shift urinary dihydroabietic acid level of 2.8 μmol/mol creatinine (95% CI 2.2-3.4). A level below 3.0 μmol/mol creatinine has been suggested as a possible biological standard.
Local exhaust ventilation is difficult to achieve with hand soldering. The ideal is probably extraction at the tip of the soldering iron. This, however, makes delicate soldering more difficult, and may cool the soldering tip. Once extracted the resins cool and solidify in fine tubing, blocking the extract. Larger printed circuit boards may obstruct the duct orifice of bench-mounted extraction. Some ducted extracts pass through filters and return the air to the work environment, rather than extract to atmosphere. The filters need to be in good condition to avoid spreading the soldering fume over the rest of the workforce.
Exposure to isocyanates is nearly always far from obvious. There is usually nothing to see, nothing to smell and often ignorance about the possible presence of isocyanates in the air. Continuous reading monitors are available for monitoring isocyanate levels in air, but sensitization can occur when exposure is well below the exposure standard. Biological monitoring is possible by measuring isocyanate-derived diamines in the urine in post-shift samples; few laboratories offer such an analysis.
19.9 Diseases associated with colophony and isocyanate exposure in the electronics industry
The first occupational exposure limit for colophony was based on its irritant effect on previously unexposed volunteers. Some 30% reported irritation to the eyes, nose and throat at a concentration of 0.07 mg/m3 (measured as the aldehyde content in the fume expressed as formaldehyde) and 5% reported irritation at 0.05 mg/m3. These concentrations are higher than have been measured in any of the electronics factories described in epidemiological studies and led to the widespread use of electronics soldering fluxes containing colophony without local exhaust extraction until the early 1980s. Nevertheless irritant-induced eye, nose, throat and airway disease is possible at high levels of exposure in the workplace.
Occupational rhinitis is common and usually precedes occupational asthma (if occupational asthma is going to develop). It improves on days away from work.
Most occupational asthma due to colophony is likely to be due to sensitization as there is a latent interval between exposure and first symptoms. Only a small proportion of the workforce is affected and sensitized workers can react to very low concentrations of colophony. Having said this, colophony fumes are more irritating than some other causes of occupational asthma such as isocyanates and they probably cause irritant reactions in those with bad asthma at concentrations that may be encountered in poorly controlled workplaces. In the 1970s when electronics components were bigger and soldering was largely uncontrolled, the mean latent interval from first exposure to first symptom was 4 years, although the variation was very wide. There was a peak within the first year of exposure and the longest recorded was 23 years. This latent interval is longer than that seen with isocyanates in the exposures at the same time.
Once sensitization had occurred, the most common reaction was for deterioration to be progressive throughout the working week with the last working day worse than the first, and with recovery starting within 1 or 2 days away from work. About 25% had equivalent deterioration each work day. Since exposures have been reduced, the progressive deterioration pattern has been less common and the equivalent deterioration pattern more common. There are some individuals who take more than 2 days to recover and do not notice improvement over a 2 day weekend away from work.
Colophony is a biological product derived from the sap of pine trees and varies in constituents depending on the source of the pine tree, but positive specific challenge testing has been shown to all the main types of colophony. The fluxes also contain activators which differ between manufacturers and, many of them being amines, may contribute to an irritant effect of the fume.
Differential challenge tests to different adducts of colophony showed reduced reactions to a methyl ester of colophony, suggesting that the carboxyl groups are important in allergen recognition (Figure 19.1).
Figure 19.1 Specific challenge tests to colophony in an electronics worker with bystander exposure to colophony flux-cored solder showing a dual immediate and late asthmatic reaction. Methylation of the colophony using a similar exposure nearly abolished the reaction
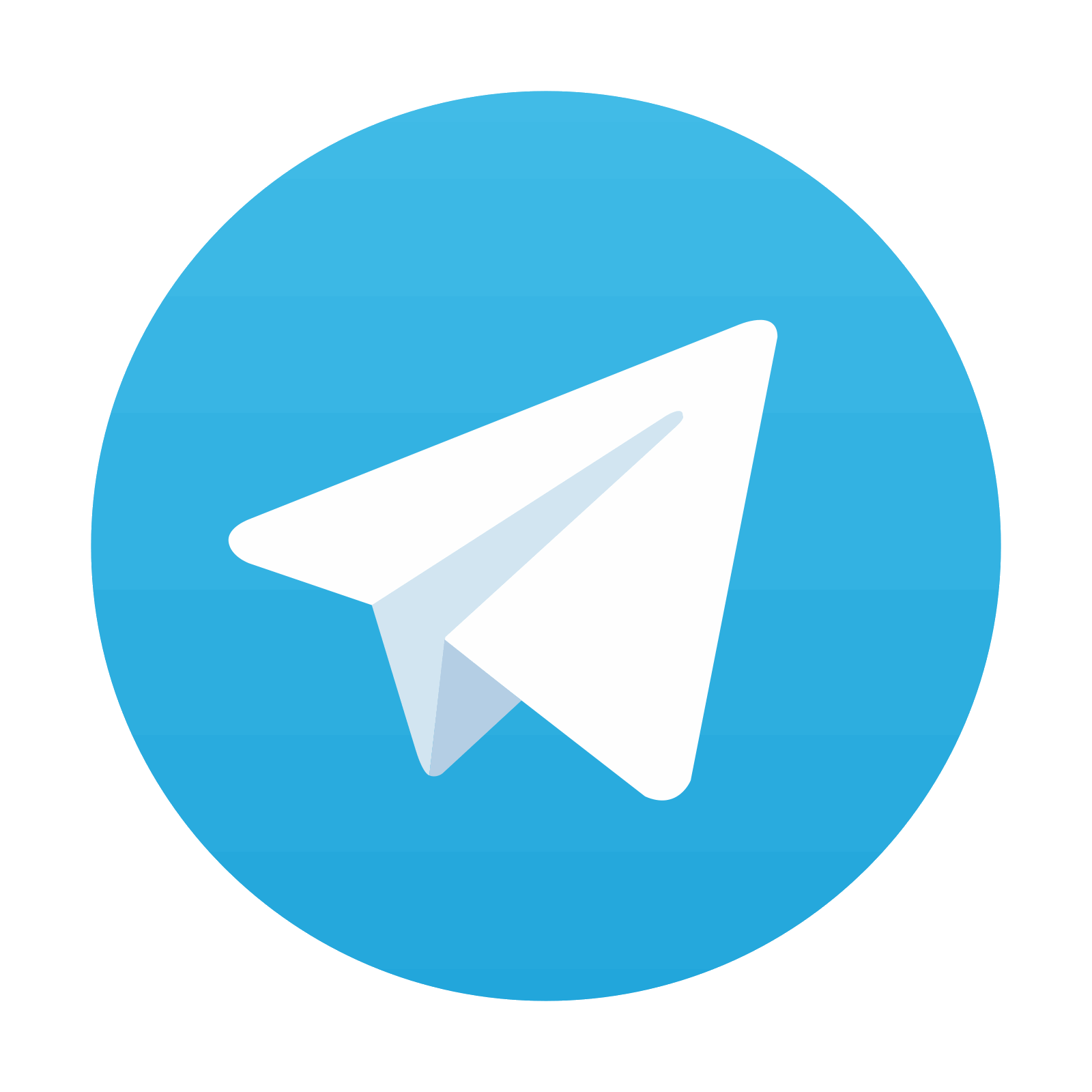
Stay updated, free articles. Join our Telegram channel
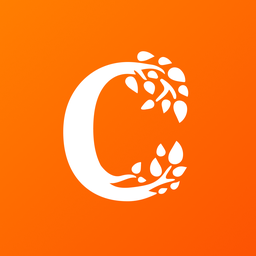
Full access? Get Clinical Tree
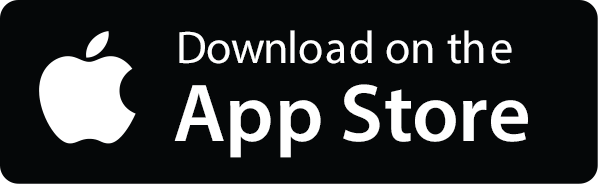
