We read with interest the brief review by Krittanawong et al., summarizing the data available regarding the implementation of Lean Six Sigma processes in the modern day catheterization laboratories . As pointed out by the authors, these strategies were originally developed in manufacturing industries and aimed to improve process efficiency as well as reduce waste products. As one could easily surmise, Lean and Six Sigma have strongly complementary strengths that could be very useful for a considerable improvement in several healthcare workflow processes. The Lean Six Sigma approach improves the operational efficiency by incorporating the diagnostic and analytical tools of the Six Sigma along with the best practice solutions for dealing with process redundancies and unnecessary time consumption.
Over the last decade, Lean Six Sigma approach has found its way into several non-manufacturing service industries including healthcare. Despite the ease of applicability of this management tool to improving a healthcare related workflow process, there is a fundamental difference between healthcare industry and other manufacturing industries. In a manufacturing industry, the client is interested only in the end product. Therefore, the factors that are considered important relate to cost-containment and maintaining the quality of the final product. The customers in healthcare are our patients. In contrast with the manufacturing industries, our customers participate in the entire process rather than enjoy the fruits of the end product. Therefore, successful implementation of management tools to improve the efficiency of a workflow process would likely improve the experience of our patients and lead to a greater “customer satisfaction”.
The workflow processes in medicine are not well designed and are characterized by unnecessary duplication of services, long waiting times and consequent delays experienced on the part of both the provider and the patient. These redundancies in several healthcare processes are a significant contributor to soaring healthcare expenditures. Operational inefficiencies plague several catheterization laboratories across the world and hence these processes have been successfully applied towards improvement in efficiency. The improvements in processes have ranged from reductions in door to balloon times in acute myocardial infarction scenarios to improvement in the turnover time for elective cases .
Besides the catheterization laboratories, the Lean Six Sigma approach has been applied to several other healthcare scenarios. Several large European hospitals have embraced Lean Six Sigma application to improve healthcare related workflow processes. Implementation of Lean Six Sigma in a large Red Cross hospital in the Netherlands was influential in reducing long waiting times in an overcrowded emergency room . In addition, the Lean Six Sigma team also recognized several workflow issues in the operating theater that contributed to inefficiencies, delays and complaints from the employees. In addition to process improvement, this application was thoroughly appreciated by the employees as a very useful instrument, thereby improving workplace morale considerably .
As has been evident from several studies including ours , there are several important facets that need to be recognized for implementing a process improvement initiative in a catheterization laboratory.
- 1.
There is always a scope for improvement in the current workflow process. It is important to be flexible and be willing to accept change.
- 2.
Collaboration between physicians, nurses, healthcare managers and business administrators is vital for process improvement.
- 3.
It is important to identify the key improvement areas and define the important performance metrics upfront before implementing a process improvement strategy.
- 4.
All process improvement strategies are “continuous” improvement strategies. It is critical to continuously monitor and alter the process, as necessary, to sustain the benefits derived from the initiative.
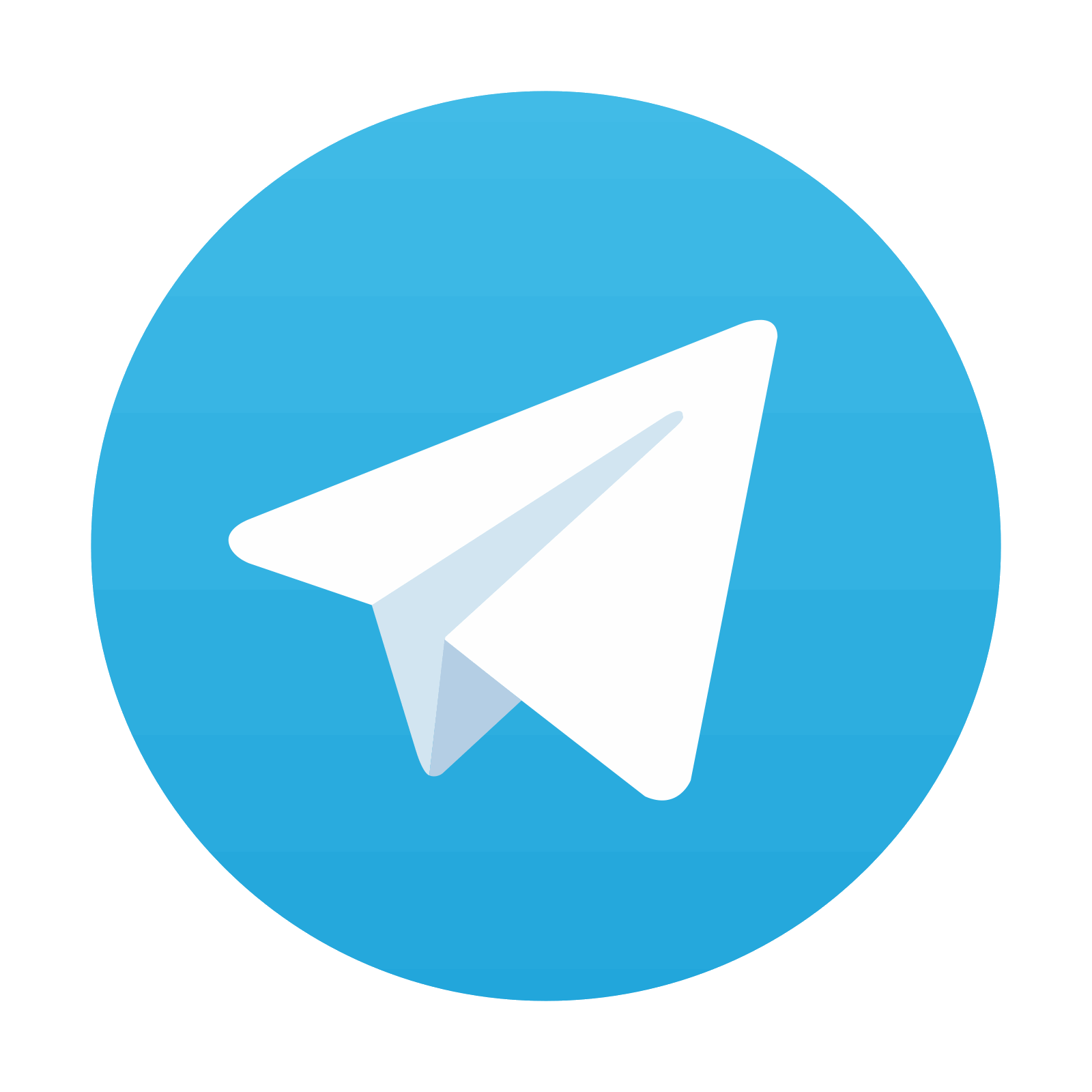
Stay updated, free articles. Join our Telegram channel
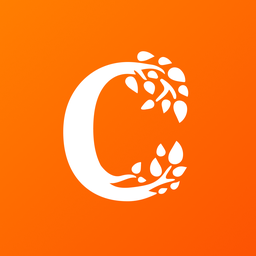
Full access? Get Clinical Tree
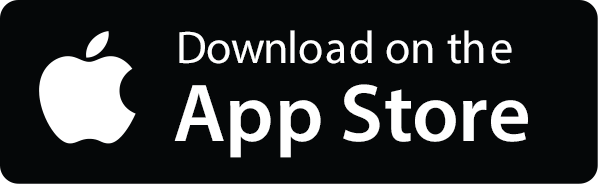
