Abstract
Valve stents are small cylindrical structures introduced in stenosed valves to replace them and restore blood flow. High radial force has become an essential feature of these stents. The primary aim of this investigation was to investigate the effects of varying stent “design parameters” on its radial force by using the finite element method (FEM). The improved model design was carried out to meet the functional and surgical requirements. The finite element model to evaluate radial force of stent was dependant on various design parameters. The results show that amplitude was the dominant parameter in this study. Increasing either strut circumference or thickness generally improved radial force of stent. However, increasing either amplitude or radius of curvature generally weakened it. In conclusion, FEM can quantify the compressive mechanical property of stent and help designers to optimize stent systems.
1
Introduction
Aortic valve stent has been increasingly used over the past few years for noninvasive treatment of aortic stenosis. The diseased valve is replaced by a biological valve which is sutured to the stent and crimped into a catheter driven through the femoral artery to the aortic parent position and deployed, thus pushing the diseased valve aside and keeping itself in position. Invariably, the stent used in this procedure undergoes enormous amount of stress caused due to the high pressures exerted by the blood flow changes in the aorta and the left ventricle. So modeling of an ideal stent design was done and then subjected to finite element analysis to understand the effects of stent strut thickness on the radial force of the stent . Because of the association between low radial force and stent failure, the relationship between radial force and stent structures has been widely investigated through the use of various methods. These testing methods can be broadly divided into the following two categories: one is that several stents have been tested by subjecting them to direct forces generated by differently shaped, rigid compression devices. The other is that several stents have been tested by subjecting them to increasing hydrostatic or gas pressure generated by rubber tube simulating the vascular. Besides the testing methodology, computational methods play an important role in the study of the mechanical properties of stent . Computational methods such as finite element modeling provide an excellent means to investigate the radial force of stent. In order to achieve more general and universally applicable results, we elected to investigate strut thickness parameters. The purpose of this investigation was to employ the finite element method (FEM) to evaluate the impact of varying design parameters on the radial force of stent.
2
Methods
2.1
Finite element models
Stent geometries were uniquely defined using the following parameters: (a) diameter of the aorta; (b) distance between the aortic root and the coronary artery roots; (c) position of the coronary arteries; (d) diameter of the coronaries; (e) stent–endothelium mechanics. With these parameters kept into consideration, an aortic valve stent was designed to suit its requirement for percutaneous replacement. Fig. 1 shows a three-dimensional geometrical model of a stent. A stent usually consists of two parts: links and rings ( Fig. 1 A); the former play an important role in the flexibility of the stent, and the latter mainly influence its radial force . Moreover, the repetitious structures (e.g., ring and link) of the stent in the longitudinal and circumferential directions allow for the extrapolation of complex stent behavior from a simplified stent model. Thus, a stent model consisting of one sixth of a ring ( Fig. 1 B) is sufficient for prediction of more complex stent behavior. Stent ring geometries were uniquely defined using the following four parameters ( Fig. 2 ): axial ring amplitude ( f ), strut radius of curvature at the crown junctions ( r ), strut width ( e ), and thickness ( t ). All stent designs had the same original outer diameter of 18 mm which was served for the aorta having a diameter of 15–16 mm.
For the purpose of this investigation, the stent models were labeled according to the design parameters incorporated within them. Names were composed based on the strut width, thickness, radius of curvature, and amplitude. Radius of curvature was given a numerical symbol with magnitude proportional to its actual value, where “1” represents 2 mm, “2” represents 2.2 mm, and “3” represents 2.4 mm. The amplitude was given an alphabetic symbol where “A,” “B,” and “C” represent 8, 8.5, and 9 mm, respectively. Similarly, the strut width was given a numerical symbol where “1,” “2,” and “3” represent 0.4, 0.5, and 0.6 mm, respectively. The strut thickness was given an alphabetic symbol where “A,” “B,” and “C” represent 0.4, 0.5, and 0.6 mm, respectively. A summary of the stent designs and corresponding parameter values studied herein is given in Table 1 . The ANSYS finite element package was used to calculate the radial force of the stent. To develop the finite element model, the stent was first modeled on Solidworks and then exported to ANSYS. The stent solid model was meshed by transferring the nodal coordinates from a Cartesian coordinate system into a cylindrical coordinate system. In this way, triangular finite element meshes were generated for the design. Apparently, degree of freedom of the device was 2.
Model | Parameters of stent model | Results | ||||
---|---|---|---|---|---|---|
Label | Radius of curvature ( r ) (mm) | Axial amplitude ( f ) (mm) | Strut width ( s ) (mm) | Strut thickness ( t ) (mm) | Maximum radial strength (NM/mm 2 ) | Radial stiffness (N/mm 2 ) |
1A1A | 2.0 | 8.0 | 0.4 | 0.4 | 1.5 | 8.3 |
2A1A | 2.2 | 8.0 | 0.4 | 0.4 | 1.2 | 4.8 |
3A1A | 2.4 | 8.0 | 0.4 | 0.4 | 1.1 | 4.6 |
2B1A | 2.0 | 8.5 | 0.4 | 0.4 | 1.4 | 2.9 |
2C1A | 2.0 | 9.0 | 0.4 | 0.4 | 1.1 | 1.4 |
2A1B | 2.0 | 8.0 | 0.4 | 0.5 | 1.5 | 5.5 |
2A1C | 2.0 | 8.0 | 0.4 | 0.6 | 1.9 | 6.8 |
2A2A | 2.0 | 8.0 | 0.5 | 0.4 | 1.5 | 5.5 |
2A3A | 2.0 | 8.0 | 0.6 | 0.4 | 1.8 | 6.6 |
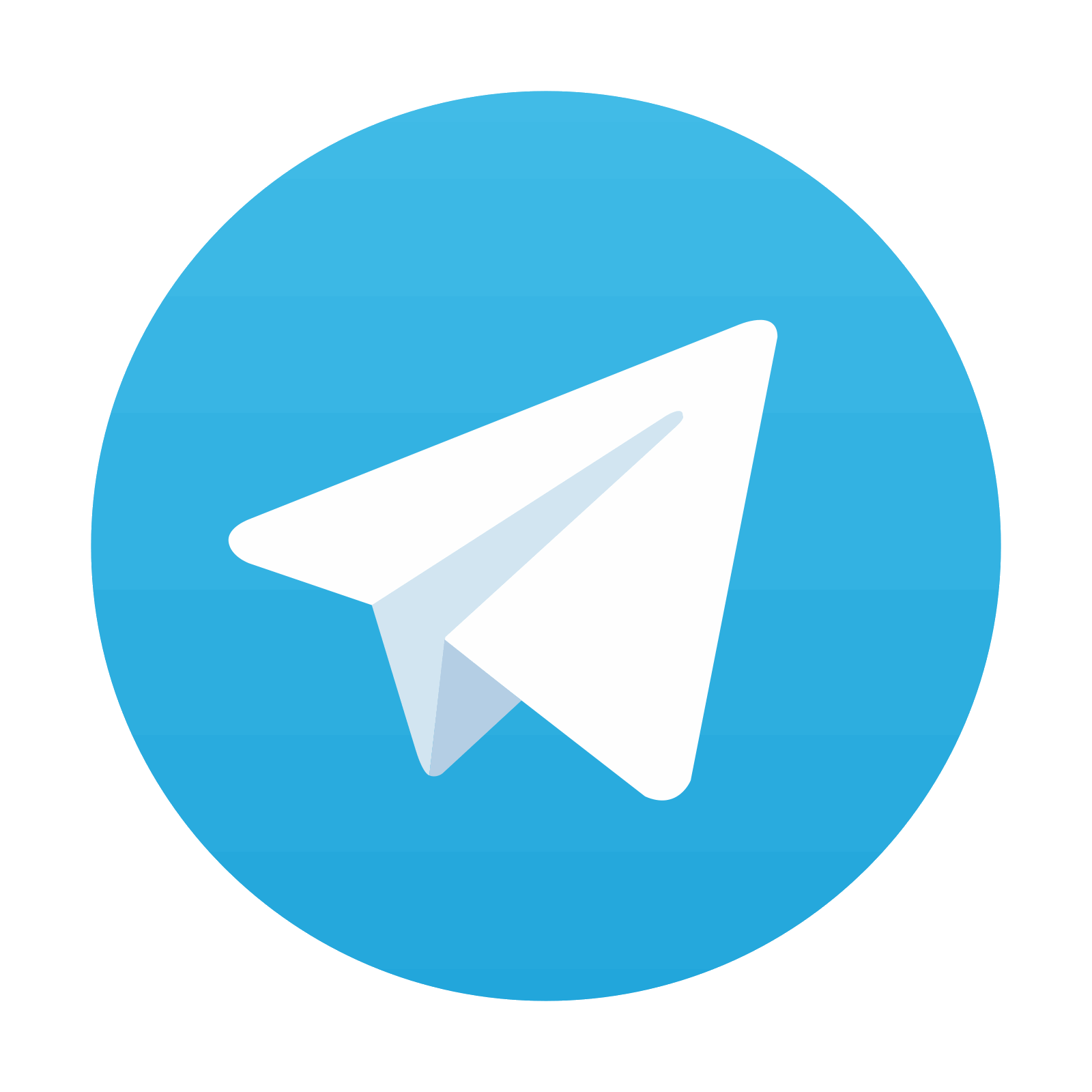
Stay updated, free articles. Join our Telegram channel
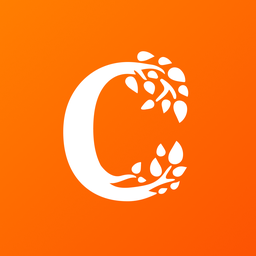
Full access? Get Clinical Tree
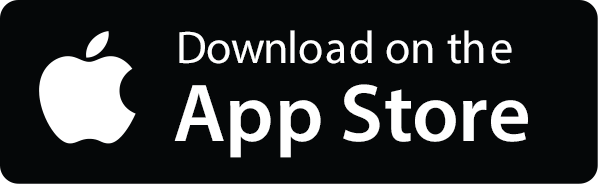

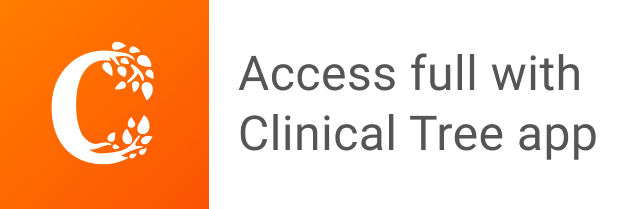