18
Chemical, coatings and plastics industries
18.1 Introduction and definitions
The overall objective of the chemical industry is to convert raw materials such as oil, gas, minerals and metals into industrial chemicals and eventually numerous consumer products (Figure 18.1). Coatings and plastics are diverse, overlapping and rapidly growing sectors of the chemical industry, and comprise the majority of the chemistry industry’s output worldwide. Coatings include a range of products such as paints, primers, varnishes and other products that protect, decorate, and/or add functionality to the surface or object being covered, such as waterproofing or protection against corrosion.
Plastics refer to synthetic or semi-synthetic polymeric materials that can be made into many different types of products, including hard and soft plastic products. Although the chemical, coatings and plastics industries encompass a wide array of different production processes, substances and products, they share some common features, exposures and respiratory risks. Primary production of coatings and plastics, the focus of this chapter, typically occurs in larger-scale chemical plants. Coating and plastic chemicals frequently then undergo additional formulation and processing in other industries, which may include final production stages, or the formulated plastic or coating may have its final application by an end-user, such as a foam applicator or spray painter. Thus exposure to coatings and plastics can occur in many other settings, such as the automotive (chapter 16), wood and textile (chapter 17), service (chapter 20), construction (chapter 21) and mining industries (chapter 13), and the home environment during home improvement projects and hobbies (Chapers 5 and 7). Many of the base chemicals used to produce coatings and plastics (e.g. acids, solvents, pigments) are used in other major sectors of the chemical industry, such as agricultural and food industries (chapter 12) and electronics (chapter 19).
This chapter is intended to help practicing clinicians understand the types of work exposures and hazards that occur in the primary chemical, coatings and plastics industries and help them recognize the respiratory disorders that can occur in workers involved in these major chemical sectors. Given the widespread use of coatings and plastics, and growing concerns regarding potential health effects, practitioners need to be familiar with major types of plastics and coatings being produced, and their potential adverse health effects. The major sectors of the chemical industry and the overall processes and potential exposures involved in the production of coatings and plastics are described first, followed by specific commonly used plastics and associated respiratory diseases. Finally an approach to diagnosis and management of workers in the chemical coating and plastics industries is summarized.
18.2 Overview of the chemical, coatings and plastics industry
The chemical industry is a large, diverse and expanding industry, with the biggest area of growth in southeast Asia. Over a million workers are currently employed in the manufacture of chemicals in the USA and over 3 million workers are employed in this sector in the European Union. Recent changes in the chemical industry, including
Table 18.1 Chemical plants: typical components and potential hazards
Component | Selected potential hazards |
Process units – reactors/distillation towers/heat exchanges/pumps | Routine and accidental release chemicals, maintenance equipment |
Storage facilities – tanks | Accidents, explosions |
Loading/unloading facilities | Accidental exposures loading and unloading chemicals |
Power sources – boilers/incinerators | Heat generation, asbestos for insulating boilers, thermal degradation products |
Warehouses – storage | Leaks, explosions |
Analytical laboratories | Novel chemical products |
Waste treatment areas | Air, soil and water contamination |
Transportation – railcars, tank trucks | Transportation accidents |
the shift in production from traditional mainly European and American countries to Asia, Latin America and eastern European countries and the development of new production technologies, may lead to new or previously unrecognized respiratory hazards.
Typical modern chemical plants are large, automated facilities that share certain common types of facilities, equipment and hazards (Table 18.1). These typically include: large tanks for chemical storage; loading and unloading facilities; power sources; storage areas; cooling towers; control rooms; process equipment; and nearby transportation facilities. There is potential for exposures during maintenance and repair of equipment, and from accidental leaks, explosions and fires. Flexible batch-production chemical plants are being built that can produce a greater number and volume of chemicals in smaller size facilities. The growth in the number and productivity of such chemical plants, combined with financial pressures to reduce costs and lax health and safety regulations, can create greater opportunities for exposure to hazardous chemicals.
18.3 Major types of paints, coatings and plastics
Paint and coating manufacturing facilities produce a large array of paints, varnishes, inks, adhesives, and specialty coatings that preserve, protect and decorate products. These include house paints, automotive finishes, appliance finishes, metallic paints and paints used for graphics and artwork.
Plastics refer to a wide range of synthetic or semi-synthetic polymerization materials or products. With advances in plastic technology and increasingly diverse uses, plastic materials are one of the fastest growing components of the chemical industry worldwide. The production of plastics involves three main steps: (1) the synthesis of plastic polymers; (2) mixing and compounding of various additives to the resin materials; and (3) conversion of the compounded polymer into different products. Common uses are in packaging and numerous consumer products, and increasingly in building and construction. Plastic materials have replaced glass, wood and metal in many industrial and commercial purposes.
Major types of plastics and coatings, their uses and chemicals used in their production are briefly discussed below, to provide clinicians with an overview of these diverse products and potential workplace exposures.
The acrylics are a group of plastics containing polymerized acrylate esters produced from acrylic monomers such as methyl methacrylate. The polymerized acrylics are used to produce glass substitutes (plexiglass), dentures, surgical prostheses, adhesives, paints and other products. The acrylic monomers are known respiratory tract irritants and sensitizing agents. Occupational asthma has been reported with several different acrylate monomers, typically in end-user settings, rather than in primary production of the acrylic components.
Acrylonitrile is an important monomer in the manufacturing of synthetic polymers such as acrylic fibers. Acrylonitrile is also copolymerized with butadiene and/or styrene to form the major synthetic rubbers in use. Acrylonitrile is an irritant to the mucous membranes and skin. Acrylonitrile is metabolized to form cyanide, which is further metabolized to thiocyanates. Therefore, acute toxicity may initially cause symptoms of headaches, lightheadedness and fatigue and rarely progresses to asphyxia and death.
Epoxy resin products are polymers formed through the reaction of uncured epoxide resins (monomers or oligomers) with a curing agent or catalyst. The uncured resin typically consists of epichlorohydrin, diluents, fillers and pigments. Diluents include glycidyl ethers of bisphenol A and various solvents. Fillers such as sand, clay or fiberglass add bulk. Common curing agents or hardeners include acid anhydrides, amines and polyamides. Major applications of epoxy resins include adhesives, laminating materials, coatings, electronics manufacturing and composite tools. Epoxy resins, similar to polyurethanes, are frequently cured where the final product is used, resulting in potentially greater exposures among end-users than among producers or formulators. Workers using epoxy resin-based paints have showed higher incidence of cough, dyspnea and cross work shift declines in FEV1 compared with unexposed workers.
The most common respiratory problem reported among workers who produce epoxy resins has been asthma, with most cases attributed to the hardening or curing agents, such as acid anhydrides, discussed further below. Exposures most commonly occur when the epoxy resin chemicals are combined and mixed or during curing, which can generate heat and fumes.
Epichlorohydrin and glycidyl ethers used to form epoxy resins such as bisphenol A epoxy are irritants at high levels, and also sensitizers, and can cause allergic contact dermatitis in exposed workers, with asthma less commonly reported.
Acid anhydrides such as phthalic anhydride, trimellitic anhydride and maleic anhydride are low-molecular weight reactive chemicals used primarily as curing or hardening agents for epoxy resins. Such reactive curing agents are also used in the production of other resins, plastics, polyesters, polyurethanes and coatings, and the production of dyes, insecticides and other products. Acid anhydrides, although best known as sensitizers, can cause severe irritation of the upper and lower airways, presenting as epistaxis or diffuse pneumonitis.
Acid anhydrides can cause several respiratory syndromes felt to be largely immunemediated, most commonly occupational asthma and rhinitis. The chemicals can react with proteins such as albumin to form antigenic complexes, and induce acidanhydride-albumin specific immune responses. Specific IgE is usually detected in workers with asthma due to trimellitic anhydride.
Exposure to acid anhydrides can also cause a hypersensitivity pneumonitis-like syndrome that has similarities to the inhalation fevers, and that has been termed late trimellitic flu. Workers present with myalgias, fever and respiratory symptoms following a work shift. An immunogenic origin for this syndrome is likely; however, direct toxicity of the acid anhydride is also possible, as well as interactions with co-exposures.
Inhalation of high levels of trimellitic anhydride has also been reported to cause a rare syndrome characterized by hemoptysis, pulmonary infiltrates, hypoxia and anemia called pulmonary disease-anemia syndrome. Lung biopsies have shown diffuse alveolar hemorrhage and edema, but the mechanism of this syndrome remains unclear.
Amines like dimethylethanolamine, piperazine and ethylenediamine are used predominantly as curing agents for resins. Some amines like hexamine are also used in the rubber industry as an accelerator. Amines can be respiratory tract irritants and also sensitizers causing occupational asthma.
18.3.6 Formaldehyde-amino resins
Formaldehyde, a reactive colorless aldehyde gas produced from methanol, is a central chemical used in the synthesis of many chemical compounds, including resins, produced by the combination of formaldehyde with melamine, urea or phenol. These resins are used in numerous applications such as foam insulation, adhesives and binders and in the production of plywood, particleboard, furniture, molded plastic, paper production and textiles. Formaldehyde also has antimicrobial properties and is used in cosmetics, formalin embalming fluid and disinfectants (Chapters 1, 4 and 20). Occupational exposures are most common in secondary exposure settings such as particleboard mills, paper or textile finishing, or disinfection or embalming, rather than primary chemical production (chapter 17).
Formaldehyde has a pungent odor and is highly irritating to the nasal and upper airways. Less commonly formaldehyde exposure can lead to asthma, and rarely inhalation of very high levels can cause chemical pneumonitis and pulmonary edema.
Asthmatic-type allergic sensitization to formaldehyde has been reported, but is not common. There is little data on the pulmonary effects of long-term formaldehyde exposures. The other major health concern regarding formaldehyde is carcinogenicity. The International Agency for Cancer Research has concluded that formaldehyde is a human carcinogen, with the strongest evidence for nasopharyngeal cancer among workers exposed to formaldehyde.
Fluoropolymers comprise a growing class of polymer materials that contain fluorine, such as polytetrafluoroethylene (PTFE), known as Teflon coating. They combine high chemical resistance with low friction, making them useful coating materials for wires, cables, metal parts and nonstick cookware.
Inhalation of the thermal decomposition of fluorocarbon polymers such as PTFE can cause polymer fume fever, similar to other inhalation fevers such as metal fume fever (see below). Exposures can occur in a variety of settings, such as welding of coated parts or among production workers who smoke, presumably from heat decomposition of cigarettes contaminated with the polymer.
Polyethylene is an important thermoplastic polymer produced from polymerization reactions involving the monomer ethylene, accounting for over 30% of the plastics produced in the USA. High-density polyethylene is used in the manufacture of containers, machine parts, toys and housewares, while low-density polyethylene is used for coatings, garbage bags and food packaging. The thermal decomposition products of polyethylene can include carbon dioxide, formaldehyde and acrolein, potent respiratory irritants. Asthma has been reported among workers heating polyethylene film as part of food-wrapping activity.
Ethylene gas is one of the most extensively produced organic compounds worldwide, used in the production of polyethylene polymers, and other common chemicals, such as ethylene oxide (a potential sensitizer), polyvinyl chloride and trichloroethylene. Historically ethylene was used as a surgical anesthetic. It can act as an asphyxiant, displacing oxygen, and can be fatal at very high concentrations.
Polypropylene is a plastic characterized by relative strength, heat resistance and durability, formed from the monomer propylene. It is used in molded products such as pipes and packaging, in fibrous forms to make clothing and carpeting, and as sheets to produce office supplies such as folders. Propylene is a simple asphyxiant and can produce symptoms of hypoxia after high accidental exposures. The thermal decomposition products of polypropylene include respiratory irritants like acrolein and formaldehyde.
Polystyrene is a polymer used to produce a wide range of rubber and plastic polymers. One of its most common uses is in the production of polystyrene foam for packaging material and food products such as plates and disposable food containers. Polystyrene is made from polymerization of the aromatic monomer styrene. Reported adverse health effects related to polystyrene production have focused largely on the irritating effects of styrene on the upper airways. Styrene has also been suggested to be a possible sensitizer.
Polyvinyl chloride (PVC) is produced by the polymerization of vinyl chloride monomer, with various plasticizers, such as phthalates and other additives. PVC is widely used in products such as plumbing pipes, cable coatings, construction composites (e.g. vinyl siding, flooring, roofing), packaging materials, housewares, electronic accessories and automotive parts.
Inhalation of PVC dust and fumes has been associated with nonmalignant respiratory diseases, including pneumoconiosis and asthma. Diffuse irregular nodular densities on chest X-ray and mild restrictive and obstructive changes in pulmonary function have been reported in workers exposed to high PVC dust levels in PVC manufacturing plants. Histologic evaluation of lung tissue from a few workers who developed pneumoconiosis has shown histiocytes, multinucleated giant cells, foreign body granulomas and fibrosis. The risk of respiratory diseases in workers exposed to PVC dust appears to be low in current operations.
Heat degradation products of PVC products can also cause respiratory irritation and probably asthma. Similar to polyethylene, ‘meat-wrappers’ asthma has been reported in workers who package food with PVC wrapping material that is heated. PVC degradation products include hydrogen chloride and various irritants, and possibly sensitizers such as phthalic anhydrides, but asthmatic responses are most likely due to the irritant exposures. There have been concerns that plasticizers and other chemicals added to PVC such as diethylhexyl phthalate may leach out of consumer products such as soft PVC toys or off-gas from home vinyl products such as flooring, but there is little data demonstrating associated health effects.
18.3.12 Polyurethanes – diisocyanates
Diisocyanates are primarily used in the production of polyurethane products, including rigid and flexible foams, coatings and paints, elastomers, adhesives and sealants The major commercial diisocyanates (commonly referred to as ‘isocyanates’) are toluene diisocyanates (TDI), methylene diphenyl diisocyanates (MDI) and hexamethylene diisocyanate (HDI), all of which can cause isocyanate asthma. Polyurethane products are used in numerous industries, including automotive, construction, furniture, paints and coatings, sports equipment and medical applications.
Diisocyanates used in polyurethane production should be distinguished from monoisocyanates such as methyl isocyanate, which contain one NCO, are not cross-linking agents and are produced for limited applications, such as pesticides. Methyl isocyanate, a potent volatile irritant, was the chemical released from a pesticide factory in Bhopal India in 1984, one of the worst recorded industrial accidents. Numerous residents living around the factory died, probably from toxic pneumonitis and pulmonary edema. Careful long-term follow-up has been difficult, but persistent respiratory symptoms, airflow obstruction and restrictive lung changes have been reported in survivors.
Isocyanates are well-known sensitizers and remain one of the most common causes of occupational asthma in industrialized countries, despite efforts to reduce airborne exposures. Most reported cases occur in end-use settings, such as spraying or when heated, rather than the primary production of isocyanates or the formulation of different polyurethane systems. In addition to respiratory exposure, skin exposure to isocyanates may also contribute to sensitization and risk for asthma. Opportunities for skin exposure are common during polyurethane production and application, such as spills, contact with contaminated equipment or direct contact with uncured or partially cured polyurethane products. Once sensitized, exposure to very low airborne levels of isocyanates, below regulatory standards, can lead to asthmatic symptoms. Preventive efforts should target respiratory and skin exposure.
Isocyanates, typically following higher respiratory exposures, can also cause hypersensitivity pneumonitis, which can overlap with asthma in the same patient. At high concentrations isocyanates can be airway irritants.
Finished cured polyurethane products, as with other plastics, are considered inert and nonhazardous. However, full curing can take longer than is apparent (tack-free), providing opportunities for unexpected exposure, especially skin exposure from handling recently made polyurethane products or coatings. Processes that generate heat such as drilling or cutting cured polyurethane materials, or fires, can generate toxic mixtures of thermal degradation products, including monoisocyanates such as methyl isocyanate and diisocyanate monomers.
18.3.13 Reactive dyes/diazonium salts
Reactive dyes are used to dye various materials, including plastics such as polyesters and nylon. The dyes contain a chromophore (the dye), and a reactive group such as vinylsulfonyl that can bind with the plastic. Diazonium compounds or salts are intermediates in the organic synthesis of reactive dyes. Reactive dyes and diazonium salts can be potent sensitizers and can cause allergic contact dermatitis and asthma. They can be difficult to identify as the causative agent, as they typically are a tiny fraction of the final product, one of many chemical substances added during production, and may not be listed on MSDS sheets or labels. They may also be used in only certain batches or production areas, making exposures more sporadic.
Table 18.2 Selected respiratory diseases related to exposures in the chemical coating and plastics industries
Respiratory disorder | Selected agents (known or suspected) |
Upper airway irritation | Numerous irritant gases, fumes, dusts, particulates (e.g. ammonia, formaldehyde, hydrogen chloride, phosgene) |
Asthma | |
Sensitizer | Isocyanates, anhydrides (e.g. trimellitic anhydride), reactive dyes |
Irritant (RADS) | Irritant gases, fumes (chlorine, formaldehyde, ammonia, sulfur dioxide) |
Acute/subacute inhalational injury | |
Toxic pneumonitis | Irritant gases, fumes (phosgene, nitrogen oxides, sulfur dioxide, smoke, thermal degradation products, mixed exposures |
Polymer fume fever | Thermal degradation fluoropolymers (polytetrafluoroethylene) |
Ardystil syndrome | Polymer textile paint (Acramin) |
Bronchiolitis obliterans | Nitrogen dioxide, diacetyl, sulfur dioxide |
Hypersensitivity pneumonitis | Isocyanates, anhydrides |
Interstitial lung disease | Polyvinyl chloride dust |
Nylon flock (Flock workers lung) | |
Asbestos (old insulation) |
18.4 Major respiratory disorders in chemical, coatings and plastics workers
Workers in the chemical, coating and plastics industries can be exposed to numerous chemicals, materials, work processes and hazards, and thus a full spectrum of occupational lung diseases can occur (Table 18.2). Acute inhalational injuries and allergic lung diseases are the most commonly recognized work-related respiratory tract illnesses in these workers. The major respiratory problems that can occur are described below.
The primary nonrespiratory occupational health problems in chemical, coating and plastics facilities, in addition to acute injuries, tend to be contact dermatitis, noiseinduced hearing loss and musculoskeletal problems.
18.4.1 Acute inhalation injury and sequelae
Exposure to a numerous chemicals used within the chemicals and plastics industry can cause a spectrum of acute inhalation injuries to the upper and lower airways (Table 18.2). These include mucosal irritation, bronchitis, irritant-induced asthma, toxic pneumonitis and pulmonary edema. The nature and extent of the injury depends primarily on the chemical agent(s) and the extent of exposure, for more severe injuries typically an accidental event. The different inhalation injury syndromes can overlap, especially as exposures are commonly mixed. In general, gases that are highly soluble in water (e.g. ammonia, chlorine and hydrochloric acid) affect primarily the upper respiratory tract, causing mucosal and eye irritation, laryngitis, bronchitis and less commonly reactive airways dysfunction syndrome or irritant-induced asthma. Such water-soluble irritant gases typically have good warning properties, so that exposures are more likely to be noticed and avoided than exposures to gases that have low water solubility (e.g. phosgene, nitrogen oxides). The later typically cause less mucosal irritation and are more likely to reach the lung parenchyma and cause chemical pneumonitis and possibly pulmonary edema.
Thermal degradation products of plastics and coatings can be particularly toxic and unpredictable. In addition to well-known toxic gases, including some that are chemical asphyxiants (e.g. hydrogen cyanide), poorly characterized mixtures of chemical fumes, gases and particulates can be released from burning plastics and coatings.
Polymer fume fever, a flu-like clinical syndrome similar to metal fume fever, can occur in workers exposed to fluorine-containing polymers such as polytetrafluoroethylene (Teflon coating) that have been over-heated. Symptoms of fever, chills, cough and dyspnea typically develop following exposure. The condition can vary in severity, probably depending on the type of pyrolysis products generated and the magnitude of exposure. Although typically self-limiting, cases that more resemble acute chemical pneumonitis, with pulmonary edema, have been reported, as well as also more longterm sequelae.
Most workers appear to recover following acute inhalation injury, whether the injury involved more the upper airways or the lung parenchyma, with improvement in symptoms and lung function over a period typically of weeks to months. However, a spectrum of lung abnormalities can persist, but current knowledge is based largely on case series and reports, and extrapolation from animal studies, rather than systematic long- term follow-up.
The most common longer-term pulmonary effect noted following acute inhalational injuries is asthmatic-type symptoms. It is likely that a spectrum of airway changes can persist after acute and subacute inhalational injuries, that include irritant-induced asthma, reactive upper airways dysfunction syndrome and gastroesophageal reflux disease.
Bronchiolitis obliterans and/or bronchiolitis obliterans organizing pneumonia (BOOP) have been reported following several chemical exposures, including sulfur dioxide, nitrogen dioxide and plastic thermal decomposition products.
Several outbreaks of unusual respiratory diseases have been reported among factory workers exposed to a variety of polymeric substances and/or chemicals. Respiratory BOOP-like disease was documented in textile workers spraying polymeric paints (Ardystil syndrome). Bronchiolitis obliterans has recently been recognized in popcorn and chemical workers exposed to diacetyl, a chemical that provides butter flavor (popcorn lung). An unusual form of interstitial lung disease (flock workers lung) has been reported in workers who process synthetic polymeric flocks. Ground glass opacities and micronodules have been reported on thin-section CT scan and pathology has shown lymphocytic bronchiolitis and peribronchiolitis with lymphoid hyperplasia.
These outbreaks, although different disease entities, highlight challenges in recognizing and preventing occupational lung diseases in workers who produce and process chemicals, coatings and plastics. In most instances, earlier cases had occurred but gone unrecognized and further evaluation of other workers revealed unrecognized disease. The outbreaks involved exposures that were presumed to be inert or previously
Table 18.3 Selected sensitizing agents in the chemical and plastics industry
Sensitizing agent | End products |
Isocyanates (TDI, MDI, HDI) | Polyurethane foams, coatings, paints |
Acid anhydrides | Paints, vanishes and reinforced plastics |
Reactive dyes and diazonium salts | Dyes or intermediates for coloration of cellulose and other fibers, plastics |
Amines (ethylenediamines, ethanolamines, piperazine) | Curing agents for plastic resins, dyes |
Acrylates | Glass substitutes, dentures, surgical prosthesis |
Azodicarbonamide, azobisformamide | Plastics |
unsuspected based on prior toxicity testing. These occupational diseases also highlight the complexity of exposures in the chemical, coating and plastics industries, including new substances substituting for older ones, mixed exposures and manipulation of inert products (e.g. cutting or sanding) generating toxic exposures.
18.4.2 Allergic diseases – occupational asthma
A number of chemicals used in the production of chemical coatings and plastics are known sensitizers that can cause occupational asthma, including isocyanates, amines, anhydrides and reactive dyes (Table 18.3). Such exposures may also cause allergic rhinitis and less commonly hypersensitivity pneumonitis. Dose-response relationships for allergenic chemicals are typically not well-defined, and once sensitized, exposure to extremely low levels can lead to asthmatic responses, complicating recognition and prevention.
Surveillance and epidemiologic studies have shown an increased risk of occupational asthma among workers in the primary chemical and plastics industries, and among end-users such as spray painters and floor layers. Such data also show that isocyanates remain the most commonly identified chemical cause of occupational asthma worldwide, despite reduced airborne exposures with the use of less volatile formulations and better hygiene practices. Skin may be an additional route of exposure, especially for chemical asthmagens, and contribute to sensitization and asthma.
18.4.3 Chronic exposures/lung diseases
The pulmonary consequences of more chronic long-term exposures in chemical, coating and plastics workers have not been adequately evaluated. Epidemiologic studies of relevant occupational cohorts are limited and have mostly focused on cancer risks, with few longitudinal studies evaluating impact on pulmonary status. The populationbased epidemiology literature investigating occupational risk factors for chronic obstructive pulmonary disease (COPD) has demonstrated that workers in industries such as plastics, textile and automotive repair have an increased risk of COPD, suggesting possible chronic effects of work exposure in such settings, but specific causative agents are not well-defined.
Data on interstitial lung diseases in chemical, coating and plastics workers are even more limited, similar to the epidemiology literature in general on interstitial lung diseases, most of which are ‘idiopathic’. Few chemicals and processes have been associated with interstitial lung diseases (Table 18.1) such as PVC dust or flock worker lung, noted above. Isocyanates and anhydrides can cause hypersensitivity pneumonitis, with almost all reported cases reflecting acute or subacute rather than chronic hypersensitivity pneumonititis.
A limited number of chemicals used to produce coatings and plastics have been shown to be carcinogenic in humans, such as vinyl chloride and chloromethyl ethers, although for several others data is controversial or inconclusive, such as formaldehyde, bisphenol A, epichlorohydrin and styrene. Spray painters have been identified as an occupation at increased risk of cancer, but the specific exposures not identified. Chemical plants, especially older ones, may contain asbestos insulation around furnaces, pipes and other structural areas.
The possibility that the workplace may be a contributing factor should be considered in any patient who works in the chemical, coating and plastic industries and presents with new or worsening respiratory complaints, especially new asthma or allergies. Most important is for the clinician to take a careful occupational history, even if the worker does not attribute his/her respiratory symptoms to work.
Medical evaluation should follow standard practices, typically first clarifying the pulmonary or nonpulmonary disorder(s) present, such as asthma. Onset of symptoms, temporal relationships of symptoms to work, days off work, and any process changes at work should be inquired about, focusing in particular on when the symptoms first started. Nonpulmonary symptoms may provide important information, such as skin rashes or neurologic symptoms. Since chemical allergies and asthma are of particular concern, history of asthma, allergies, dermatitis and eczema should be determined. Whether co-workers have had similar problems should also be determined.
Information regarding work exposures is most commonly obtained from a careful occupational history, including description of the process and workplace, known exposures, time periods worked and use of personal protective equipment. Material safety data sheets and/or labels should be reviewed to identify potential causative chemicals, remembering that such information may be incomplete and/or inaccurate.
Nonoccupational exposures and smoking history should also be clarified. Additional tests that can confirm association between work exposures and the patient’s disease, such as immunologic assays, peak flow recordings, should be considered, following standard guidelines for diagnosis.
For patients who present with acute inhalational injuries following a specific defined accidental exposure event at work, such as an accidental spill or fire, the critical task is for the clinician to best determine the nature and extent of the toxic exposures and anticipate and treat delayed or prolonged health effects. Follow-up with careful assessment of lung function is important.
Disease management should follow standard practice and treatment guidelines, also considering public health and preventive considerations. For example, if occupational asthma due to a sensitizer is diagnosed, avoiding further exposure is recommended (including skin exposure), ideally by modifications in the workplace, or a job transfer away from exposure with medical protection. Surveillance of other workers to detect similarly affected workers should be considered, as well as preventive measures to reduce exposures.
Further reading
Atis, S., Tutluoglu, B., Levent, E. et al. (2005) The respiratory effects of occupational polypropyleneflock exposure. Eur. Respir. J. 25: 110-117.
Bernstein, I.L., Chan-Yeung, M., Malo, J.L. et al.. (eds) (2006) Asthma in the Workplace and Related Conditions, 3rd edn. Taylor & Francis: New York.
Blomqvist, A., Duzakin-Nystedt, M., Ohlson, C.G. et al. (2005) Airways symptoms, immunological response and exposure in powder painting. Int. Arch. Occup. Environ. Health 78: 123-131.
Camus, P., Nemery, B. (1998) A novel cause for bronchiolitis obliterans organizing pneumonia: exposure to paint aerosols in textile workshops. Eur. Respir. J. 11: 259-262.
Eckardt, R.E. (1976) Occupational and environmental health hazards in the plastics industry. Environ. Health Perspect. 17: 103-106.
Grammer, L.C., Shaughnessy, M.A., Zeiss, C.R. et al. (1997) Review of trimellitic anhydride (TMA) induced respiratory response. Allergy Asthma Proc. 18: 235-237.
Malo, J., Hae-Sim, P., Bernstein, I. (2006) Other chemical substances causing occupational asthma. In Bernstein, I.L., Chan-Yeung, M., Malo, J.L. et al.. (eds) (2006) Asthma in the Workplace and Related Conditions, 3rd edn. Taylor & Francis: New York.
Markowitz, S. (2005) Chemicals in the plastics, synthetic textile, and rubber industry. In Textbook of Clinical and Environmental Medicine, Rosenstock, L. et al.. (eds). Elsevier Saunders: Philadelphia, PA.
Nemery, B. (1996) Late consequences of accidental exposure to inhaled irritants: RADS and the Bhopal disaster. Eur. Respir. J. 9: 1973-1976.
Redlich, C.A., Bello, D., Wisnewski, A.V. (2007) Health effects of isocyanates. In Environmental and Occupational Medicine, Rom, W.N. (eds). Lippincott-Raven: Philadelphia, PA.
Shusterman, D.J. (1993) Polymer fume fever and other fluorocarbon pyrolysis-related syndromes. Occup. Med. 8: 519-531.
Studnicka, M.J., Menzinger, G., Drlicek, M. et al. (1995) Pneumoconiosis and systemic sclerosis following 10 years of exposure to polyvinyl chloride dust. Thorax 50: 583-585; discussion 589.
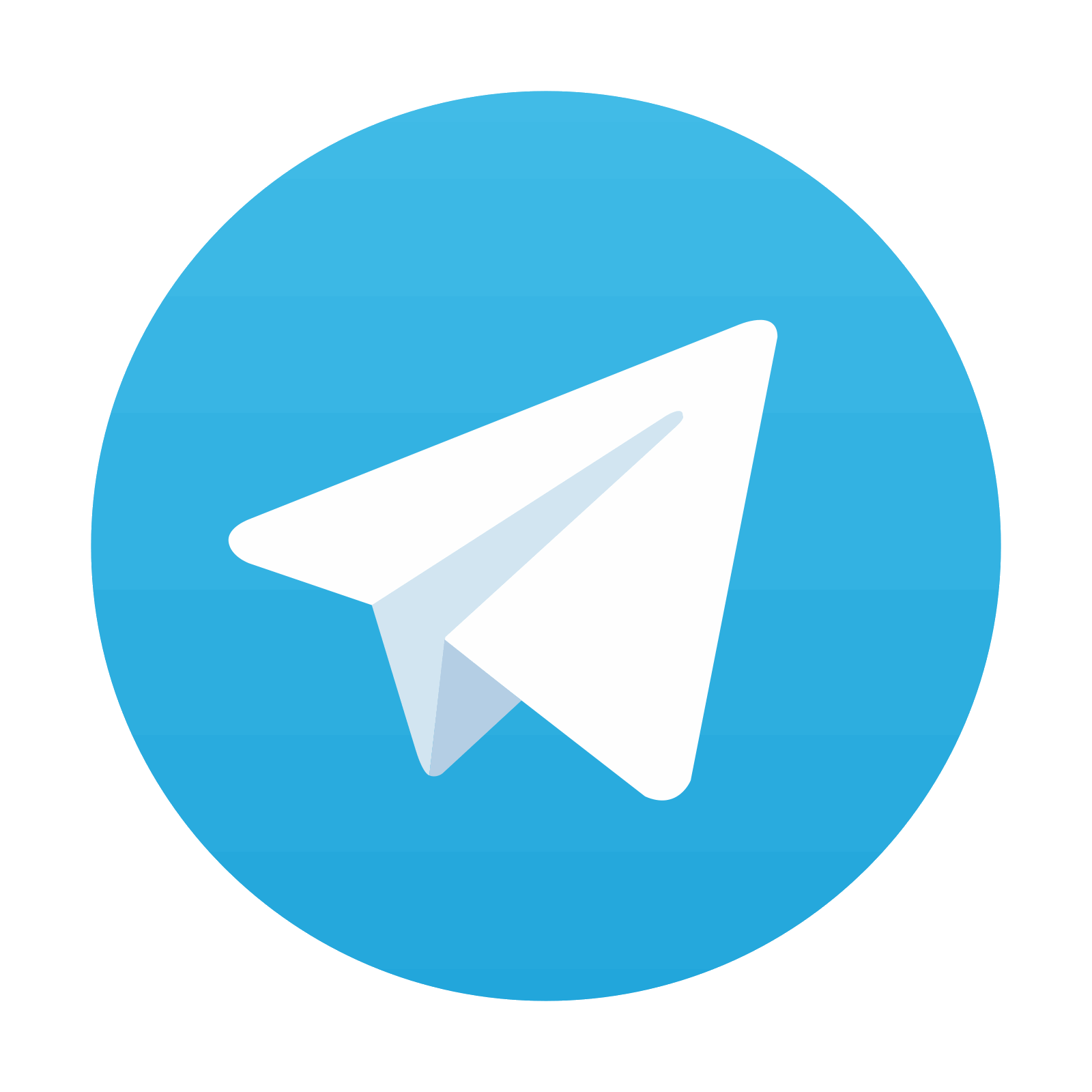
Stay updated, free articles. Join our Telegram channel
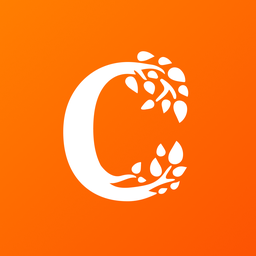
Full access? Get Clinical Tree
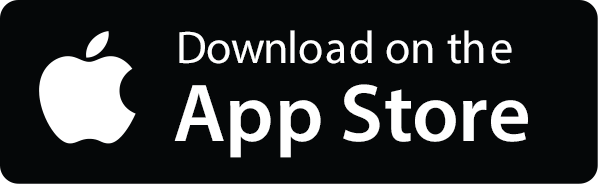
