16
Automotive industry
The production of automobiles and trucks is a major worldwide industry. There are approximately 4 million auto and truck production workers worldwide with major growth in the industry occurring in Asian-Pacific countries. Historically vehicle production was vertically integrated within one company. That company would manufacture most of their own metal and plastic parts and then assemble them into vehicles. This business model has shifted in the last couple of decades, with in-house parts manufacture being spun off as independent companies so that now 75% of autoworkers work for companies that produce vehicle parts and 25% work for companies that assemble the final vehicles. Since vehicle production is a worldwide industry, the percentage of workers in vehicle assembly vs vehicle parts production in any given country varies. Of the 1 million autoworkers in the USA, 75% are in vehicle parts manufacturing facilities; in contrast, in Belgium almost 90% of vehicle workers work in assembly facilities. This distribution between vehicle assembly and parts manufacturing is important from the health care provider’s perspective. Vehicle parts manufacturing has significantly more respiratory hazards since it involves processes such as casting metal parts in foundries, machining metal parts, manufacturing foam products and extruding and injecting plastic into molds. In contrast, vehicle assembly requires a great deal of material handling as the various parts are assembled into the final vehicle. Accordingly the major health concern in vehicle assembly facilities involves musculoskeletal conditions. However, there are respiratory concerns in assembly facilities. Important activities in vehicle assembly that generate respiratory hazards are welding, painting and the use of adhesives. Another contrast between parts manufacture and assembly is that vehicle assembly facilities are more likely to be larger corporate entities: six corporations produce 75% of the world’s vehicle production while just in the USA there are 5000-8000 vehicle parts manufacturers. This difference in corporate structure would suggest that the larger assembly facilities will have more expertise and resources to address health and safety issues than many of the smaller vehicle parts manufacturers.
This chapter will examine the respiratory hazards in vehicle assembly and parts manufacturing. The respiratory hazards of car maintenance and repair are discussed in chapter 15. Table 16.1 summarizes by vehicle manufacturing industry type (vehicle assembly vs vehicle part manufacturing) and activity (casting, welding, etc.) the possible exposures (isocyanate, silica, etc.) and the respiratory conditions (silicosis, asthma, etc.) that have been associated with these exposures in the vehicle manufacturing industry.
16.2 Respiratory hazards and disease
Both obstructive and restrictive diseases occur from exposures in the vehicle manufacturing industry. With increased automation, substitution with alternative materials and better engineering and ventilation controls, restrictive lung disease such as asbestosis and silicosis have become less common. One restrictive lung disease in the vehicle manufacturing industry whose incidence is not decreasing is hypersensitivity pneumonitis. The increase in the use of water-based synthetic metal-working fluids has caused repeated outbreaks of hypersensitivity pneumonitis. The association between metal-working fluids (MWFs) and hypersensitivity pneumonitis was first recognized in the mid 1990s. Although the same microbial agent has been identified in the MWF in a number of the outbreaks from different facilities, this agent has not always been identified during outbreaks and it has also been identified in facilities without outbreaks. A lack of understanding of what are the other important factors that initiate these outbreaks has limited the ability to reduce the respiratory hazard from MWFs. Additionally, the introduction of new technology has caused recognition of a new restrictive lung condition, nylon flock disease.
Most new cases of respiratory disease currently being identified in the vehicle production industry are obstructive: asthma, chronic obstructive pulmonary disease (COPD) and chronic bronchitis. The use of chemical sensitizers such as isocyanates, chronic exposure to irritants such as during welding and the occurrence of obstructive changes with repeated exposure to substances classically associated with restrictive disease such as silica are all causes for these obstructive lung conditions.
Lung cancer is increased among foundry workers making vehicle parts. Historically, there has been exposure to three carcinogens in the foundry environment: asbestos,benzopyrene from the fumesof the molten metaland silica. There are studies reporting a cancer risk from exposure to natural (straight) metal-working fluids (mineral oils), with the best evidence of an association between MWFs and cancer being for laryngeal cancer and the nonrespiratory cancers of bladder, pancreas, rectal, scrotum and skin.
Vehicle manufacturing workers, as other blue collar workers, generally have a higher prevalence of cigarette smoking than the general population. This increased prevalence of smoking in conjunction with workplace exposures such as silica or welding will increase the likelihood of lung cancer, COPD, chronic bronchitis and irritant symptoms more so then if the group only smoked cigarettes or only had the workplace exposures.
16.3 Vehicle parts manufacturing
Foundries produce metal parts by pouring molten metal into molds, which traditionally have been made from sand. In order to create internal cavities in the metal pieces being produced, cores made from sand are produced and placed in the mold prior to pouring in the molten metal. A common binder used in making sand cores is methylene diisocyanate (MDI). After the metal hardens the mold and core must be removed and the metal smoothed. The activity of removing the mold and core is conducted in the ‘finishing’ or ‘clean’ room. Activities there include knocking off the sprue (hardened metal from where the pour goes into the mold), shake-out and chipping and grinding. Figure 16.1 shows a picture of an individual chipping and another grinding an engine block. Both workers are wearing respirators because air levels are above the allowable OSHA permissible exposure levels. During pouring, the molten metal heats the silica. Because heated silica is transformed into more fibrogenic forms, tridymite and cristobalite, and the removal of sand generates a large dispersion of particulates, the ‘cleaning’ area of a foundry is the location with the highest risk for silica exposure. Silica exposure is also significant in the mold and core areas and among any workers responsible for handling and cleaning up spilt sand. Asbestos exposure has occurred among workers maintaining furnaces, pipes and cupolas (the latter being the containers in which molten metal from furnaces are transferred to the molds). The workers who maintain and repair furnaces and pipes are in some facilities classified as ‘skilled trades’: insulators, electricians, plumbers and millwrights. Removal of fire bricks in furnaces and cupolas is a high-risk job for both asbestos and silica exposure. Furnaces are typically relined on a regular basis and, in the USA until the 1980s, workers on overtime from throughout the facility would on weekends and downtime throughout the year work in the furnaces chipping away the firebrick and asbestos insulation without adequate respiratory protection.
Figure 16.1 An individual chipping and another grinding an engine block. Both workers are wearing respirators because air levels are above the permissible exposure levels
There is substantial data that the mineral dusts, particularly silica, cause obstructive as well as restrictive disease. These obstructive changes are more prevalent in workers who also have smoked cigarettes. Silica exposure also increases the risk of active tuberculosis and silica is considered a risk factor, like diabetes or steroid use, when considering the indications for treating latent tuberculosis or the number of medications needed when treating active tuberculosis. Other conditions increased in silica-exposed workers are chronic renal failure and connective tissue diseases, particularly scleroderma and rheumatoid arthritis. Even in the absence of clinical disease, markers of connective disease including antinuclear antibody and rheumatoid factor are more prevalent in patients with silicosis.
There are multiple methods for forming sand molds and cores. A common method involves the mixture of TEA gas (tetraethylamine) and MDI. Ruptured or disconnected hoses, causing acute exposure, are not uncommon in this work setting. Acute exposure after such a rupture or spill may cause an acute chemical pneumonitis. With recovery from the acute episode, the worker may be left with persistent shortness of breath and wheezing. On testing these patients may have a positive methacholine challenge test and meet the diagnostic criteria for reactive airway dysfunction syndrome. Exposure to TEA gas is associated with difficulty in vision, particularly being able to see at night. MDI is a common cause of sensitization and work-related asthma. This method is a ‘cold’ method. An alternative method is a hot process involving a phenolic-formaldehyde resin. Formaldehyde exposure from this process is a cause of work-related asthma.
Alternative foundry processes, such as lost wax casting, or lost foam casting, that do not use silica or use less silica and do not use known sensitizers, have become more common in recent years. The risk of silicosis is also less in aluminum foundries.
The International Agency for Research on Cancer has classified iron and steel founding as a group I human carcinogen: sufficient evidence of carcinogenicity in humans. Similar group I classifications have been given for asbestos, benzo(a)pyrene and silica, to which foundry workers have been commonly exposed. The US National Toxicology Program does not classify work processes such as foundries but has classified asbestos and silica as ‘known human carcinogens’ and benzo(a)pyrene as ‘reasonably anticipated to be a human carcinogen’. Asbestos and silica exposure in foundries is described above; benzo(a)pyrene is one of the polynuclear aromatic compounds produced with combustion and is formed when metal is heated, so that workers in the pouring areas of a foundry would have the potential for the greatest exposure.
Metal pieces need to be cut, drilled, shaped and smoothed. In order to facilitate this machining, MWFs are used. These substances are commonly called ‘coolants’, but their primary properties are actually to remove metal particles, protect or treat the surface of the metal being machined and prolong the life of the machining equipment. Figure 16.2 shows a machining operation with an MWF being used. There are four types of metalworking fluids, straight (natural, mineral oil), emulsified, semi-synthetic and synthetic fluids. Straight fluid, as the name implies, is 100% mineral oil and generally is what was used prior to the 1970s. Water-based oils are now more commonly used; emulsified oil is an emulsion of mineral oil and water; semi-synthetic contains smaller amounts of mineral oil than the emulsified oils; and synthetic oils contain no mineral oils. Since these are water-based products, corrosion inhibitors as well as dyes and biocides to inhibit microbiological growth are found in the three types of nonstraight MWFs. Typically these fluids are collected in sumps around the machining operations and repeatedly reused in the machining process after the metal particles are filtered out. Specific personnel are designated to check the pH, assess the biological content and put in additives in response to the sampling results. Work around water-based MWFs is associated with a higher prevalence of respiratory symptoms, chronic bronchitis and doctor visits than work around the straight fluids. Individual components of waterbased metal-working fluids, such as ethanolamine compounds, have been shown by specific antigen bronchoprovocation testing to cause work-related asthma, while microbiological contamination of nonstraight MWFs has been associated with outbreaks of hypersensitivity pneumonitis.
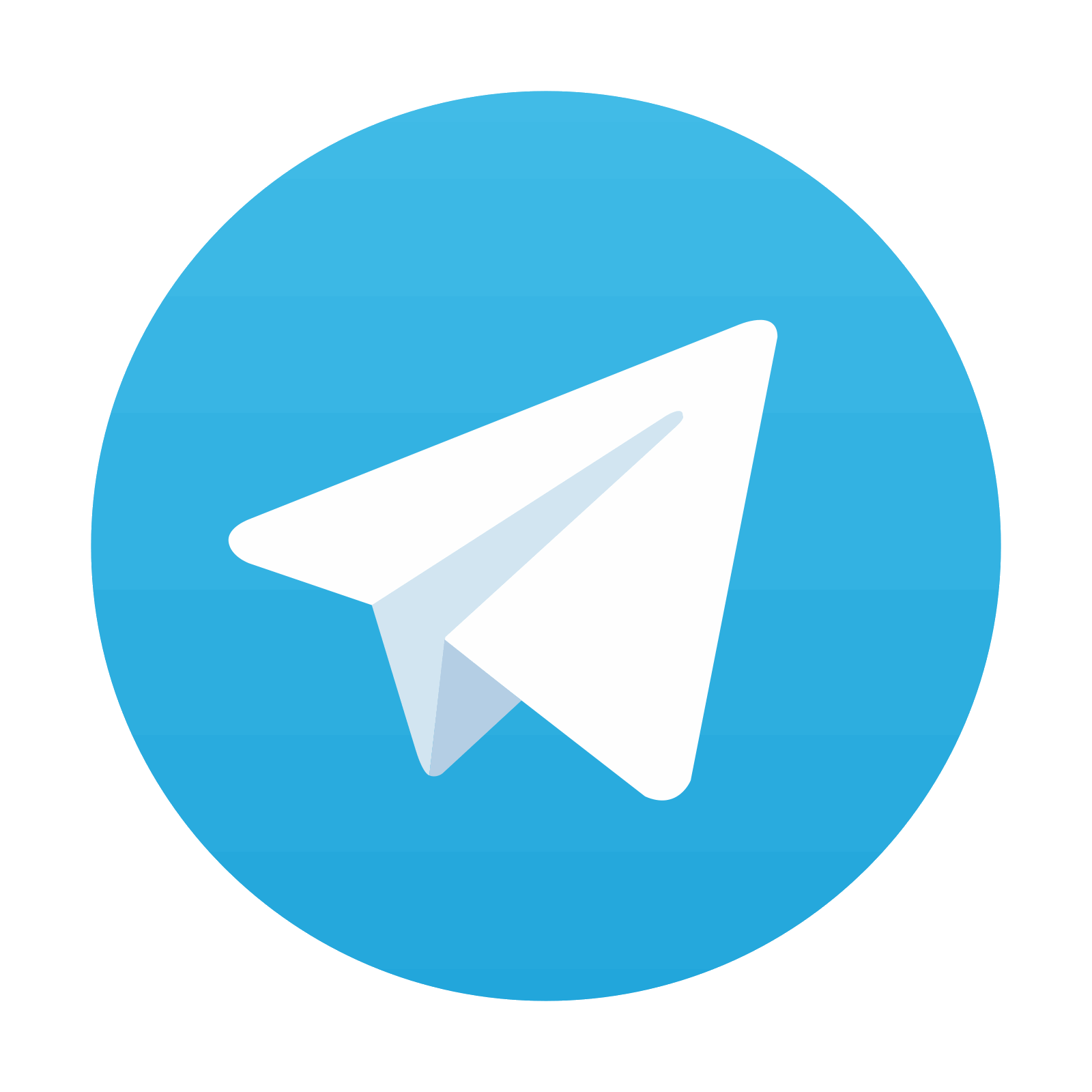
Stay updated, free articles. Join our Telegram channel
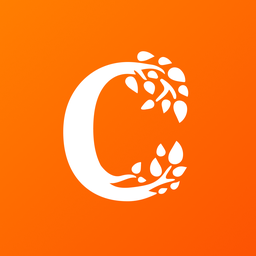
Full access? Get Clinical Tree
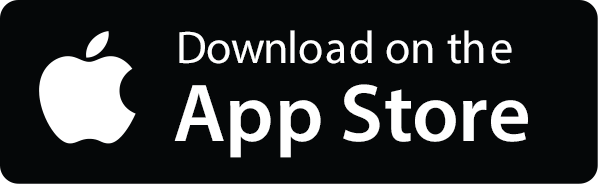
